8D-Methode & 8D-Report: Problemlöser für Unternehmen
Jeder, der in einem produktiven Umfeld arbeitet, weiß, dass Probleme unvermeidlich sind. Doch wie gehen wir am besten mit diesen Situationen um? Wie stellen wir sicher, dass wir nicht nur Probleme lösen, sondern auch proaktive Maßnahmen ergreifen, um zukünftig ähnliche Fälle zu vermeiden? Ein hilfreiches Tool: die 8D-Methode.
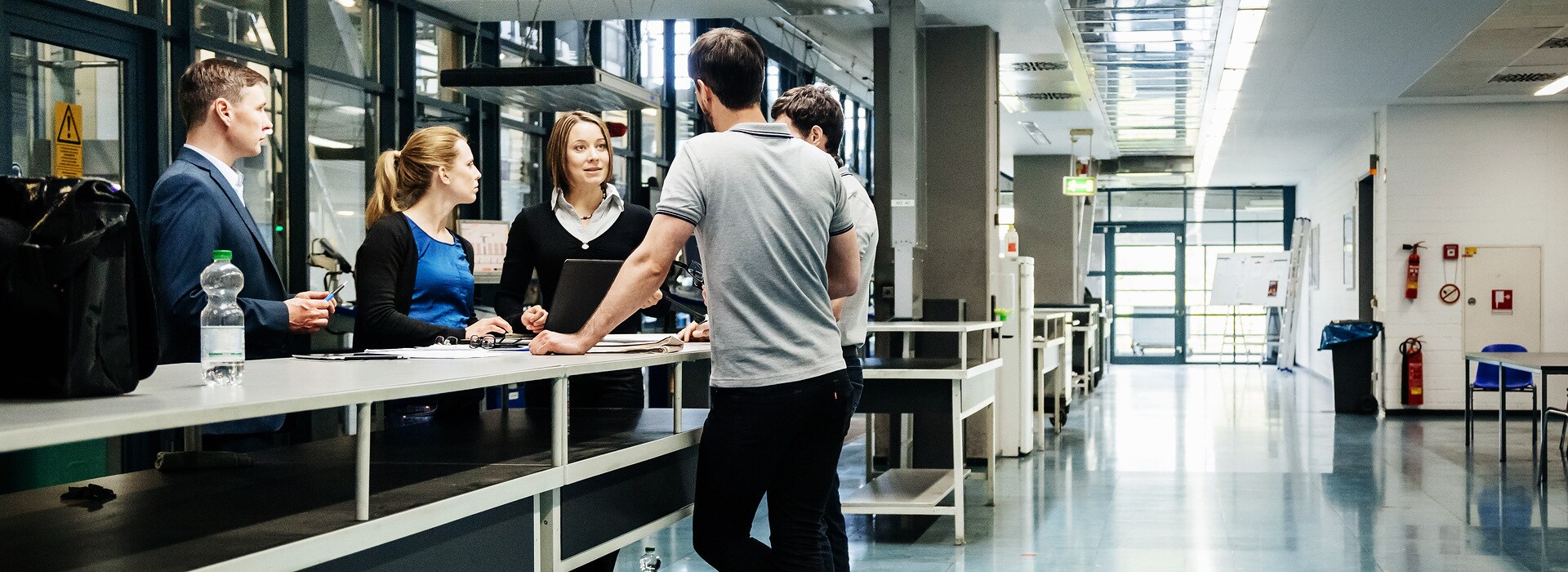
Themen in diesem Artikel
Mit dem 8D-Report dauerhaft Qualität sichern
Die 8D-Methode ist ein strukturierter Problemlösungsansatz, der Unternehmen hilft, Probleme und daraus resultierende Herausforderungen effektiv zu bewältigen. Wir stellen Ihnen nicht nur die 8D-Methode allgemein vor, sondern geben Ihnen auch Einblicke in unsere eigenen Erfahrungen bei Wilo. Finden Sie heraus, wie die 8D-Methode Ihre Arbeit verbessert und wie sie Ihr Unternehmen stärken kann.
Woher kommt die 8D-Problemlösungsmethode?
Jeder Prozess, jede Technik und jedes Konzept haben ihre Wurzeln, auch die 8D-Methode. Sie wurde ursprünglich 1974 als Problemlösungsmethode vom US-amerikanischen Verteidigungsministerium entwickelt und standardisiert. Einige Jahre später suchte der Automobilhersteller Ford nach einem ähnlichen Modell. Bei Ford wollte man damit wiederkehrende Probleme und Kundenbeschwerden effektiv und nachhaltig lösen – mit Erfolg. Schnell wurde die Methode zu einem effektiven Instrument zur Fehlerbeseitigung in verschiedenen Branchen. Seitdem ist sie integraler Bestandteil des Qualitätsmanagements in zahlreichen Unternehmen.
Was ist die 8D-Methode?
Die 8D-Methode ist ein strukturiertes Vorgehen zur Fehlerbeseitigung in acht Schritten. Der Begriff 8D steht für 8 Disziplinen, die die Grundlage für diesen Prozess bilden. Ihr Ziel: Probleme systematisch analysieren, Lösungen finden und Maßnahmen zur Vorbeugung zukünftiger Probleme ergreifen. Es ist also nicht nur eine Methode zur Fehlerbehebung, sondern vielmehr ein Instrument zur kontinuierlichen Verbesserung und Vorbeugung.
Welchen Nutzen schafft die 8D-Methode?

Marius Richter, Group Director Supplier Quality
In der Geschäftswelt können Probleme immer wieder auftreten. Mit der 8D-Methode können Unternehmen jedoch sicherstellen, dass ein Problem nur einmal auftritt. Fehler lassen sich damit nachhaltig beheben. Für Marius Richter, Group Director Supplier Quality bei Wilo, besteht eine effektive Fehlerbehebung, darin einen strukturierten Ansatz zur Problemlösung zu verfolgen und die Teams dazu zu befähigen, Probleme eigenständig, effizient und vor allem dauerhaft zu lösen. „Seit wir die 8D-Methode eingeführt haben, haben wir eine deutliche Verbesserung in unserer Produktionskette bemerkt. Um Produktionsunterbrechungen und Quality Incidents weiter zu minimieren, bewerten wir die 8D-Berichte nun. So können wir nachhaltig die Premiumqualität von Wilo gewährleisten“, erklärt Marius Richter.
Was ist ein 8D-Report?
Kernstück der 8D-Methode ist der 8D-Report, auch 8D-Bericht genannt. Dieser standardisierte Bericht enthält acht Kapitel zur Aufnahme aller Informationen, die im Laufe des Prozesses gesammelt werden. Er dient als zentrales Kommunikationsmedium, sowohl intern als auch zwischen Kunden und Lieferanten.
Wilo hat diese Problemlösungsmethode für seine Prozesse übernommen und speziell an die spezifischen Anforderungen angepasst. Entstanden ist ein Template für den 8D-Report, das nach den acht Schritten der Methode strukturiert ist.

Der 8D-Report im Überblick
D1: Teamzusammenstellung
Im ersten Schritt des 8D-Prozesses wird ein multidisziplinäres Team zusammengestellt. Hierbei werden verschiedene Perspektiven, Erfahrungen und Fähigkeiten zusammengebracht, die eine umfassende und effektive Problemlösung ermöglichen.
D2: Problembeschreibung
Je präziser ein Problem beschrieben ist, desto näher ist man bereits an der Lösung. Daher besteht der zweite Schritt aus einer Problembeschreibung, die allen Beteiligten das gleiche Verständnis ermöglicht. Dieser Schritt ist entscheidend, da Missverständnisse und Fehlinterpretationen die Effektivität der Problemlösung beeinträchtigen können.
D3: Sofortmaßnahmen
Damit sich unmittelbar negative Auswirkungen eines Problems minimieren lassen, werden in Schritt drei Sofortmaßnahmen ergriffen. Diese können beispielsweise Sortiermaßnahmen, manuelle Kontrollen oder schnell umsetzbare automatisierte Prozesse sein. Dadurch lassen sich Unterbrechungen vermeiden und sicherstellen, dass Produktionsprozesse weiterlaufen.
D4: Ursachenanalyse
Oftmals liegen einem Problem tiefere Ursachen zugrunde. Die effektive Lösung eines Problems erfordert daher auch die Identifizierung der Hauptursache. In Schritt vier werden daher Analysetechniken wie 5-Why oder Ishikawa eingesetzt, um die Wurzeln des Problems zu ergründen.
D5: Mögliche Korrekturmaßnahmen
Nachdem die Ursachen des Problems identifiziert wurden, diskutiert und testet das Team in Schritt fünf potenzielle Verbesserungsmaßnahmen. Dieser Schritt ist kollaborativ und erfordert eine aktive Teilnahme aller Beteiligten.
D6: Maßnahmen Implementierung
Sobald die geeigneten Maßnahmen ermittelt wurden, werden sie in Schritt sechs implementiert. Jede Maßnahme erhält ein spezifisches Datum, bis zu dem sie umgesetzt sein muss. Dabei werden sie ständig auf ihre Wirksamkeit hin geprüft.
D7: Präventive Maßnahmen
Schritt sieben ist der Blick in die Zukunft: Welche „Lessons Learned“ nehmen die Beteiligten mit und wie lässt sich auf Basis dieser Erfahrungen ein Wiederauftreten verhindern? Wie kann das Erreichte beibehalten werden? Zudem wird der Anwendungsbereich erweitert und ähnliche Produkte oder Prozesse proaktiv überprüft. Gegebenenfalls werden die gleichen Maßnahmen an anderer Stelle implementiert, um zu verhindern, dass der gleiche Fehler in anderen Bereichen auftreten kann.
D8: Abschluss
Schließlich werden in Schritt acht die Ergebnisse dokumentiert und wichtige Lektionen für die Zukunft herausgestellt. Ein weiterer Aspekt: Der Dank ans Team. Diese Wertschätzung fördert die Motivation und das Engagement der Teammitglieder und schafft einen positiven Abschluss des 8D-Prozesses.
Welche Praxiserfahrung hat Wilo mit der 8D-Methode gemacht?
Durch den strukturierten Ansatz der 8D-Methode hat Wilo die Anzahl der Produktionsunterbrechungen reduziert. Aber auch die hohe Produktqualität konstant sichergestellt. „Die 8D-Methode ist ein wesentlicher Bestandteil in unserem Tagesgeschäft. Sie stellt sicher, dass wir unseren hohen Qualitätsanspruch erfüllen und gleichzeitig unseren Lieferanten die Möglichkeit geben, ihre Qualität zu verbessern. Gerade weil die 8D-Methode insbesondere im Automobilbereich bekannt und gefordert ist, nutzen wir diese hohen Standards auch für unsere Branche“, erklärt Marius Richter.
Wie hat Wilo die 8D-Reports individualisiert und optimiert?
Wilo hat die 8D-Methode individualisiert und für sich weiter optimiert, indem eine Bewertungsmatrix eingeführt wurde. Dieses zusätzliche Instrument geht über den bekannten Standard hinaus und sorgt dafür, dass die 8D-Berichte von Anfang an den Erwartungen des Unternehmens entsprechen. Die klare Kommunikation dieser Anforderungen an die Lieferanten ist ein entscheidender Erfolgsfaktor.
Zusammenfassung: Nachhaltiges Qualitätsmanagement mit der 8D-Methode
Die 8D-Problemlösungsmethode und ihre erfolgreiche Anwendung bei Wilo ist ein wertvolles Instrument für die effektive Problemlösung und Prozessverbesserung. Sie strukturiert den Fehlerbeseitigungsprozess und stellt sicher, dass Lösungen nachhaltig sind. Darüber hinaus hilft 8D auch, die Kommunikation innerhalb des Unternehmens und zwischen Kunde und Lieferant zu verbessern. Mit ihrem einheitlichen Berichtsformat werden alle Informationen transparent geteilt und Maßnahmen klar kommuniziert. Vor allem aber liegt die Stärke der 8D-Methode darin, die Prozessverbesserungskultur zu fördern. Langfristig lässt sich mit dieser Methode die Premiumqualität der Produkte sicherstellen.