How businesses learn from mistakes: 8D Report and Eight Disciplines Problem Solving Method
Anyone who works in a productive environment knows that problems are inevitable. But how do we best deal with them? How do we ensure that we not only resolve problems, but also take proactive measures to avoid similar cases in the future? The 8D methodology is a helpful tool.
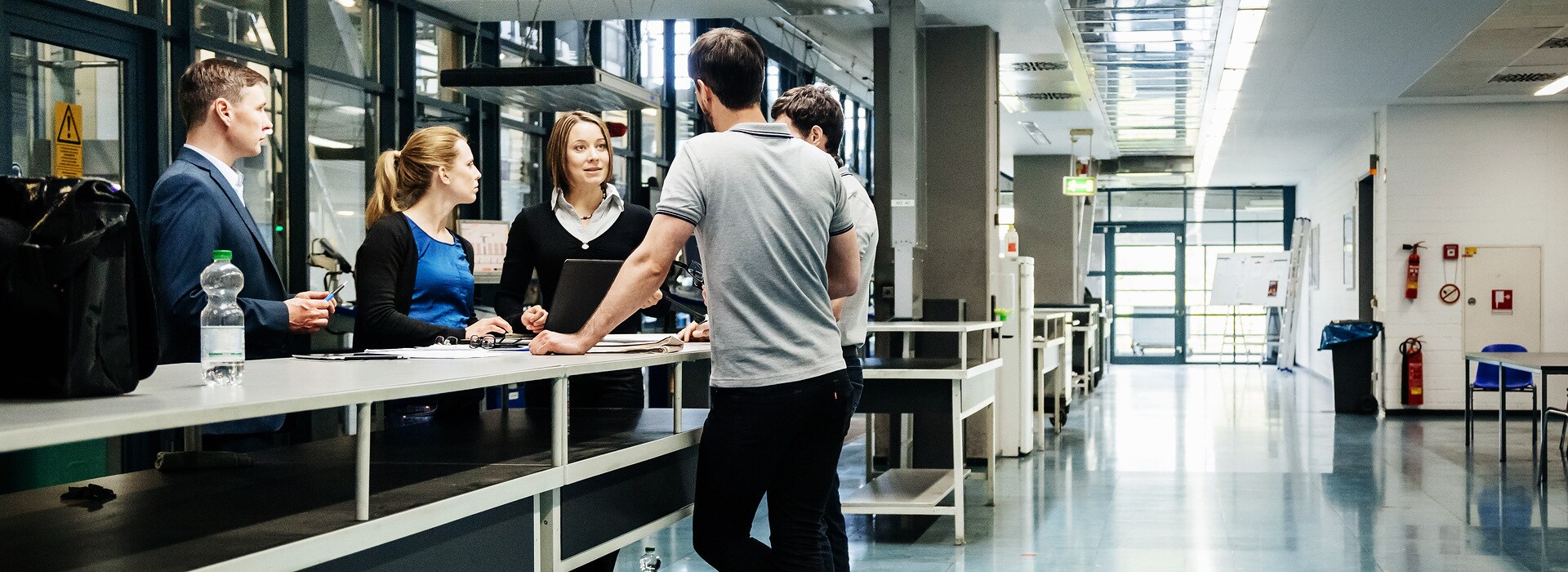
This article features
8D enables enduring top quality
The 8D methodology is a structured problem-solving approach that helps companies effectively manage problems and the resulting challenges. We will not only introduce you to the 8D methodology in general but will also give you insights into our experiences with it at Wilo. Find out how the 8D methodology can improve your work and how it can strengthen your business.
Where does the 8D methodology come from?
Every process, every technique and every concept has its roots. The 8D methodology is no different in this respect. It was originally developed and standardised as a problem-solving method by the US Department of Defense in 1974. The Ford Motor Company was looking for a similar model a few years later. At Ford, the aim was to solve recurring problems and customer complaints effectively and sustainably – and they were successful. The methodology quickly became an effective tool for troubleshooting in various industries. Since then, it has become an integral part of quality management in numerous companies.
What is the 8D methodology?
The 8D methodology is a structured approach to troubleshooting in eight steps. The term 8D stands for the 8 disciplines that form the basis for this process. Their objective: to systematically analyse problems, find solutions and take measures to prevent future problems. It is therefore not merely a methodology for troubleshooting, but rather a tool for continuous improvement and prevention.
What benefits does the 8D methodology bring?

Marius Richter, Group Director Supplier Quality
In the business world, problems can arise again and again. However, with the 8D methodology, companies can ensure that a problem only occurs once. Errors can thus be sustainably eliminated. For Marius Richter, Group Director Supplier Quality at Wilo, effective troubleshooting consists of taking a structured approach to problem solving and empowering teams to solve problems independently, efficiently and, above all, permanently. “We’ve noticed a significant improvement in our production chain since the 8D methodology was introduced. To further minimise production downtime and quality incidents, we now evaluate the 8D reports. In this way, we can guarantee Wilo’s premium quality over the long term”, explains Richter.
What is an 8D report?
The 8D report forms the core of the 8D methodology. This standardised report contains eight chapters to record all the information collected during the process. It serves as a central communication medium, both internally as well as between customers and suppliers.
Wilo has adopted this problem-solving method for its processes and adapted it to its specific requirements. The result is a template for the 8D report structured according to the eight steps of the methodology.

The 8D report at a glance
D1: Team formation
In the first step of the 8D process, a multidisciplinary team is created. This brings together different perspectives, experiences and skills that enable comprehensive and effective problem solving.
D2: Problem description
The more precisely a problem is described, the closer one is to the solution. Therefore, the second step consists of describing the problem in such a manner that all parties understand it in the same way. This step is crucial as misunderstandings and misinterpretations can influence the effectiveness of problem solving.
D3: Interim containment action
To minimise the immediate negative effects of a problem, direct action is taken in step three. This can include sorting measures, manual controls or automated processes that can be implemented quickly. In this way, interruptions are avoided and production can continue.
D4: Root cause analysis
Often there are deeper reasons behind a problem. Effectively resolving a problem therefore also requires you to identify the root cause. In step four, therefore, analytical techniques such as “five whys” or Ishikawa are used to get to the root of the problem.
D5: Developing corrective actions
After identifying the causes of the problem, the team discusses and tests potential improvement measures in step five. This step is collaborative and requires the active participation of all stakeholders.
D6: Implementing corrective actions
Once the appropriate actions have been identified, they are implemented in step six. Each action is given a specific deadline by which time it must be implemented. Their effectiveness is repeatedly checked in the process.
D7: Preventive measures
Step seven is to look into the future: What lessons learned do those involved take with them? How can a recurrence be prevented based on these experiences? How can what has been achieved be maintained? In addition, the scope of application is expanded and similar products or processes are proactively reviewed. If necessary, the same measures are implemented elsewhere to prevent the same error from occurring in other areas.
D8: Conclusion
Finally, step eight documents the results and highlights important lessons for the future. And not to forget: A thanks to the team. This appreciation promotes the motivation and commitment of the team members, and the 8D process comes to a positive conclusion.
What practical experience has Wilo had with the 8D methodology?
Wilo has been able to reduce production downtime through the structured approach of the 8D methodology. And high product quality is also continuously ensured. “The 8D methodology is an essential part of our daily business. It ensures that we meet our high-quality standards. At the same time, it gives our suppliers the opportunity to improve their quality. Precisely because the 8D methodology is known and demanded by the automotive industry, we also set these high standards for our industry”, explains Richter.
How has Wilo customised and optimised 8D reports?
Wilo has customised the 8D methodology and further optimised it for itself by introducing an evaluation matrix. This additional tool goes beyond the established standards and ensures that the 8D reports meet the company’s expectations right from the start. Clearly communicating these requirements to suppliers is a critical success factor.
Summary: Sustainable quality management with 8D
The 8D methodology as successfully implemented at Wilo is a valuable tool for effective problem solving and process improvement. It structures the troubleshooting process and ensures that solutions are sustainable. Furthermore, 8D also helps to improve communication within the company as well as between customer and supplier. With its uniform reporting format, all information is shared transparently and measures are communicated clearly. Above all, the strength of the 8D methodology lays in the fact that it promotes our culture of process improvement. In the long term, this methodology ensures the premium quality of the products.